A Comprehensive Guide to the Process and Advantages of Plastic Extrusion
In the huge realm of production, plastic extrusion emerges as a extremely effective and essential procedure. Altering raw plastic into continual accounts, it accommodates a plethora of markets with its amazing adaptability. This overview intends to elucidate the complex actions associated with this approach, the sorts of plastic proper for extrusion, and the game-changing benefits it gives the market. The following discussion promises to unfold the real-world influences of this transformative procedure.
Recognizing the Fundamentals of Plastic Extrusion
While it may show up facility at very first glimpse, the procedure of plastic extrusion is basically basic. The process begins with the feeding of plastic material, in the form of granules, powders, or pellets, into a heated barrel. The shaped plastic is after that cooled, strengthened, and reduced into wanted lengths, finishing the process.
The Technical Process of Plastic Extrusion Explained

Types of Plastic Suitable for Extrusion
The selection of the right kind of plastic is an important facet of the extrusion procedure. Various plastics use special properties, making them a lot more suited to particular applications. Polyethylene, for instance, is typically utilized as a result of its low cost and simple formability. It supplies excellent resistance to chemicals and moisture, making it optimal for products like tubing and containers. Similarly, polypropylene is one more prominent choice because of its high melting factor and resistance to tiredness. For even more robust applications, polystyrene and PVC (polyvinyl chloride) are frequently chosen for their strength and resilience. These are usual alternatives, the selection eventually depends on the certain requirements of the item being produced. Comprehending these plastic types can significantly improve the extrusion procedure.
Contrasting Plastic Extrusion to Other Plastic Forming Methods
Understanding the kinds of plastic suitable for extrusion leads the way for a more comprehensive conversation on how plastic extrusion stacks up against various other plastic developing approaches. Plastic extrusion is unrivaled when it comes to producing continual profiles, such Recommended Site as seals, pipelines, and gaskets. It also enables for a constant cross-section along the size of the product.
Trick Benefits of Plastic Extrusion in Manufacturing
In the world of manufacturing, plastic extrusion uses several considerable benefits. One notable advantage is the cost-effectiveness of the procedure, which makes it an economically attractive production method. In addition, this method offers remarkable item flexibility and enhanced manufacturing rate, consequently increasing overall manufacturing performance.
Economical Manufacturing Technique
Plastic extrusion leaps to the forefront as a cost-efficient production method in manufacturing. In addition, plastic extrusion needs less power than standard production techniques, adding to reduced operational prices. In general, the financial advantages make plastic extrusion an extremely eye-catching choice in the production sector.
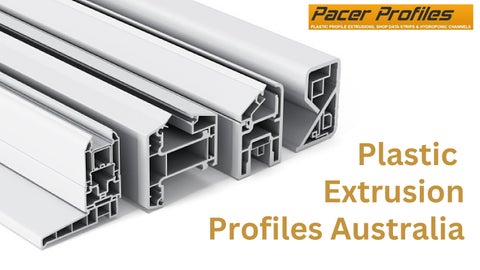
Superior Product Flexibility
Beyond the cost-effectiveness of plastic extrusion, one more considerable advantage in making hinge on its superior product adaptability. This procedure enables for the production of a large range of products with varying forms, designs, and dimensions, from basic plastic sheets to intricate profiles. The adaptability is connected to the extrusion die, which can be tailored to generate the desired item design. This makes plastic extrusion a suitable option for industries that require customized plastic elements, such as vehicle, building and construction, and packaging. The capacity to create varied items is not only useful in conference specific market demands however additionally in enabling producers to discover brand-new product with very little capital expense. Essentially, plastic extrusion's item versatility fosters innovation while boosting functional effectiveness.
Boosted Production Speed
A significant benefit of plastic extrusion exists in its enhanced manufacturing speed. Couple of various other production procedures can match the speed of plastic extrusion. In addition, the capacity to keep consistent high-speed production without compromising item quality sets plastic extrusion apart from various other methods.
Real-world Applications and Impacts of Plastic Extrusion
In the realm of production, the technique of plastic extrusion holds extensive relevance. This procedure is extensively utilized continue reading this in the production of a selection of items, such as plastic tubing, home window frameworks, and weather condition removing. As a result, it considerably influences industries like building, packaging, and auto sectors. Its effect expands to everyday products, from plastic bags to toothbrushes and disposable cutlery. The economic advantage of plastic extrusion, mostly its high-volume and affordable outcome, has reinvented production. The ecological effect of plastic waste continues to be a concern. The industry is persistently aiming for developments in naturally degradable and recyclable materials, suggesting a future where the benefits of plastic extrusion can be maintained without endangering environmental sustainability.
Conclusion
To conclude, plastic extrusion is a highly reliable and efficient technique of changing basic materials into diverse products. It offers countless advantages over various other plastic developing methods, consisting of cost-effectiveness, high result, minimal waste, and layout flexibility. Its effect is greatly felt in different markets such as building and construction, vehicle, and durable goods, making it an essential procedure in today's production landscape.
Delving much deeper right into the technological process of plastic extrusion, it starts with pop over here the option of the suitable plastic material. Once cooled down, the plastic is cut right into the needed sizes or wound onto reels if the product is a plastic film or sheet - plastic extrusion. Comparing Plastic Extrusion to Various Other Plastic Forming Methods
Understanding the types of plastic appropriate for extrusion paves the means for a broader conversation on just how plastic extrusion stacks up versus other plastic creating approaches. Few other manufacturing processes can match the rate of plastic extrusion.